Prototype Tooling
Low-Cost Molds for physical prototypes
Looking for a production partner that moves at your speed? Our prototype tooling enables true functional prototyping and a more efficient development process. Ready to test different plastic materials? We’ve got you covered. With prototype tooling from BeraTek Industries, you can validate your injected molded parts early, saving time, reducing risk, and improving final product outcomes.
Benefits of Using a Prototyping Tool
Prototype tooling offers significantly faster turnaround than traditional hard tooling, bringing you closer to your final design in less time. These molds are also easier to modify, allowing for design flexibility and reducing costs throughout the development process.
Or call (844) 237-2835
Process
Prototype Tooling Steps
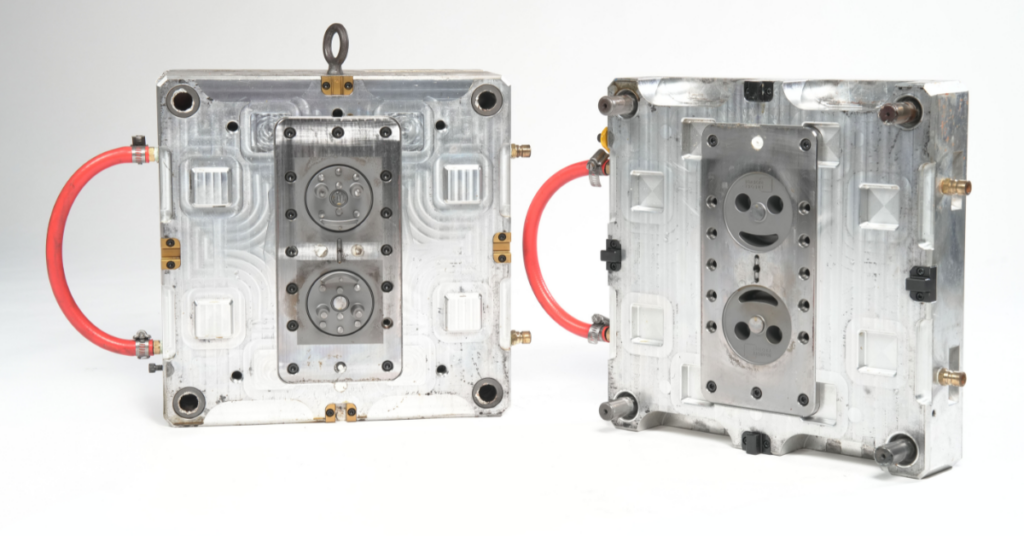
Design
Machining
Testing
Iteration
Prototype vs Bridge Tooling
Prototype and bridge tooling are critical phases in product development, providing a cost-effective way to refine designs and evaluate functionality before full-scale production. These tools allow you to visualize the product, make necessary design adjustments, and test parts using production-intent materials, ensuring accuracy and performance ahead of final manufacturing.
Prototype Tooling
Prototype tooling is a cost-effective, no-frills solution for producing parts early in the development process. These tools are built with simplified configurations, such as cut-in steel cores and minimal cooling features, and typically use a single cavity machined directly into the mold block rather than interchangeable inserts. Prototype tooling enables efficient testing and validation while keeping upfront costs low.
Bridge Tooling
Bridge tooling is an ideal solution for producing parts in volumes that exceed prototyping needs but don’t yet justify the investment in full-scale production tooling. It’s perfect for small-to-medium batches and helps you move forward quickly without the long lead times or high costs of full-scale production. Whether you’re testing the market or waiting on final tools, bridge tooling fills the gap.
Key Differences
Before transitioning to full production, it’s essential to develop and test your plastic products for fit, form, and function. Discover the key differences between prototype and bridge tooling, and how each can help refine your design for a higher-quality final product.
Quality
Prototype tooling is used as a learning tool—great for early testing, but the parts produced may not meet every quality or performance standard needed for final use. The process is experimental, and the tooling isn’t built for high-volume production. Bridge tooling is designed with more durability and consistency in mind, allowing for better-quality parts that are closer to final production standards.
Volume
Prototype tooling is used for low-volume runs during the early stages of production, which is when you just need a small batch of parts to test things out early on. Bridge tooling is used for medium-volume runs, which is when you need more parts—enough to keep things moving but not quite full production levels yet.
Prototype Tooling FAQs
What is prototype tooling?
What is prototype injection molding?
What is the difference between tooling and molding?
What is the difference between hard tooling and soft tooling?
How many parts can you get from a prototype tool?
Streamline Your Path to Production
BeraTek Industries is here to guide you through the transition to larger-scale production, making any necessary adjustments for longer-term success. As your trusted early-stage development partner, we’ll help you we’ll make incremental modifications to refine both individual parts and entire products, ensuring a seamless path from prototype to final production. Let’s work together to bring your vision to life.
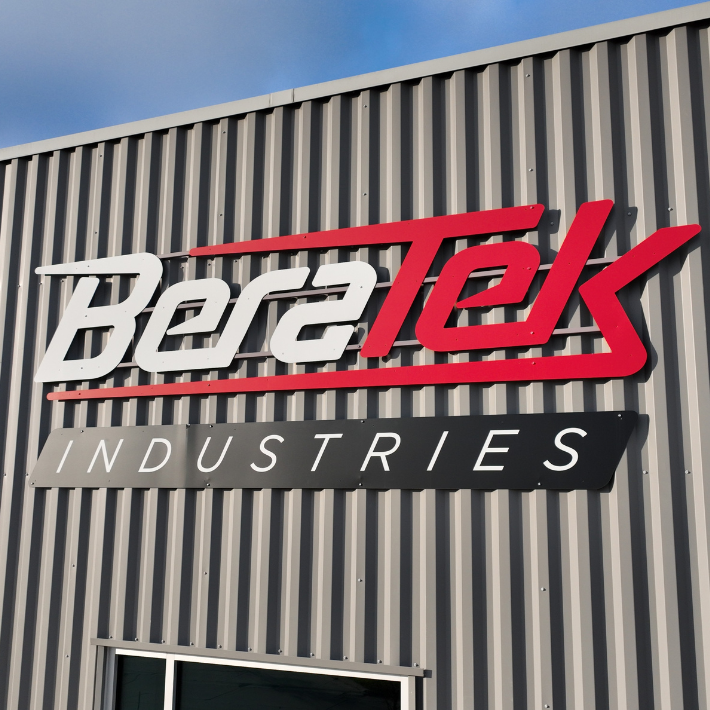