Tool Building
INjection mold Tooling Solutions for Every Need
Whether you need straightforward fixtures or intricate molds, our tools are engineered to ensure both durability and efficiency. We understand the demands of modern manufacturing environments and deliver solutions that meet those rigorous standards.
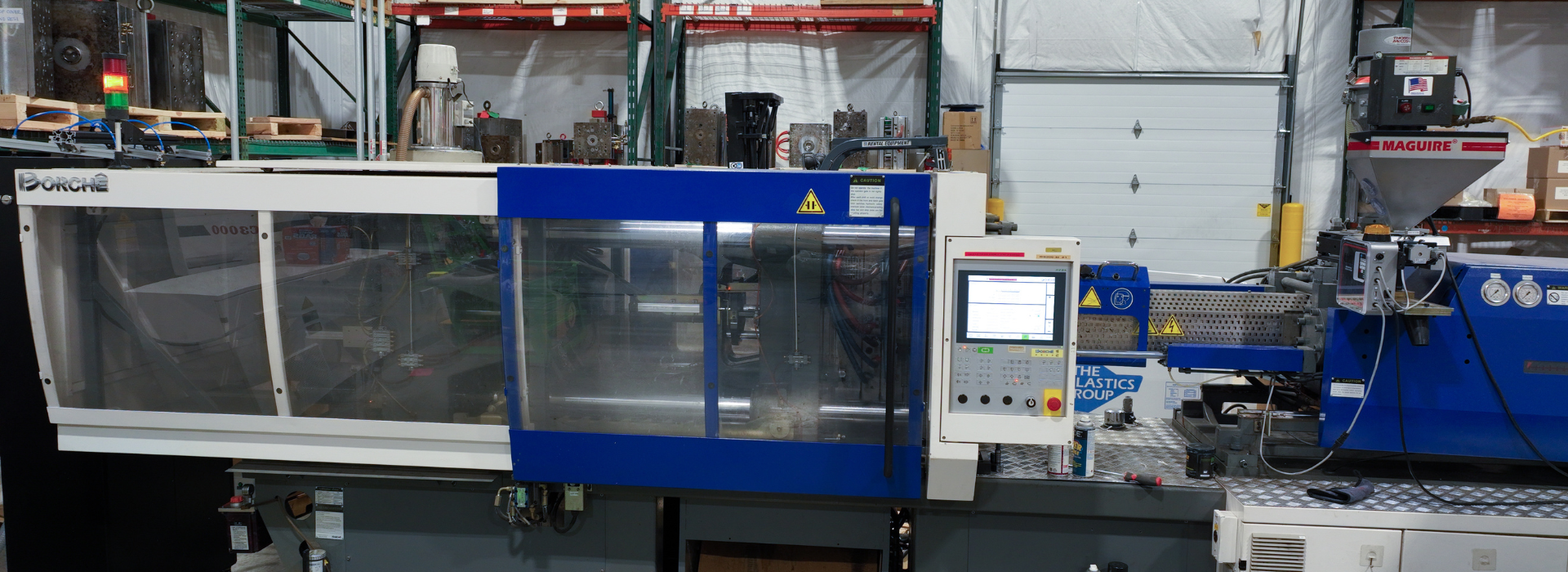
Our Work
Precision tool building is the cornerstone of achieving superior manufacturing results
Achieve more with our advanced expertise in tooling design and manufacturing to drive your success. We engineer your parts for seamless production, applying cutting-edge techniques and precision at every stage to optimize performance and efficiency.
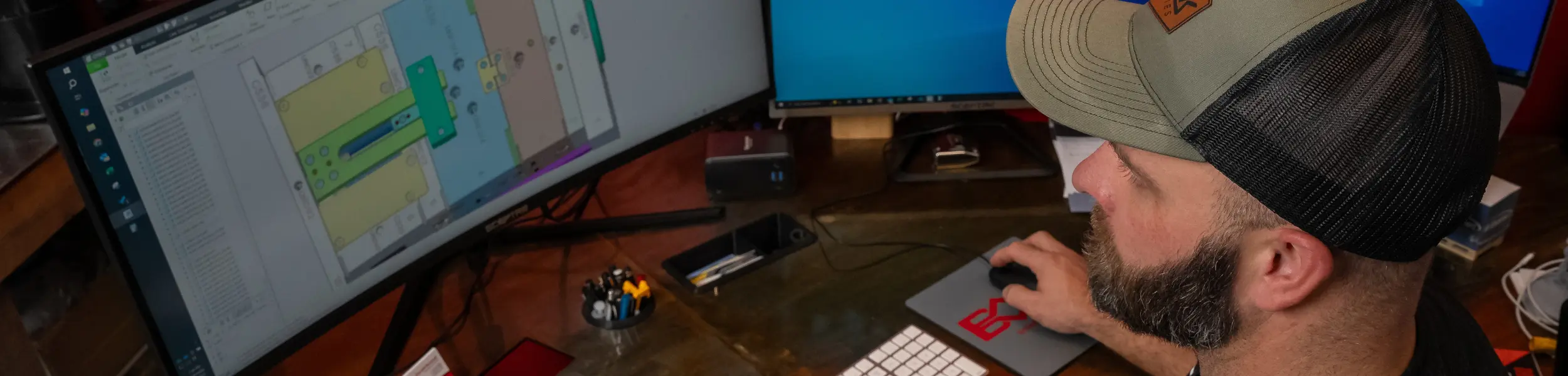
Expertise
Tool Building Services
Injection molding relies on precise tooling to ensure accuracy and consistency. With various configurations designed for specific production needs, selecting the right injection molding tooling is essential for project success. Partnering with an experienced injection molding team ensures the right expertise to optimize performance, efficiency, and quality.
Prototype & Bridge Tooling
Our prototype and bridge tooling solutions offer a fast, cost-effective way to refine designs, materials, and molding processes before full-scale production. Prototype tooling enables quick iterations for market readiness, while bridge tooling provides an affordable transition to full production, ideal for market trials and scaling up efficiently.
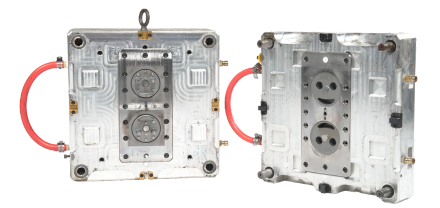
Production Tooling
Our production tooling services provide high-quality tools designed for large-scale manufacturing. Engineered for durability and efficiency, these tools ensure consistent, reliable production and repeatability of high-volume parts.
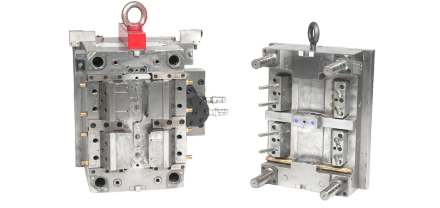
MUD Base Tooling
MUD base (Master Unit Die) tooling offers a versatile and economical solution for smaller parts or lower volume projects. By using a standard master frame and interchangeable inserts, MUD base tooling reduces costs and lead times.
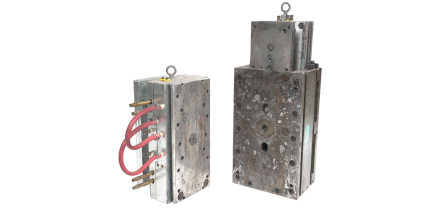
Production Tooling Options
Family Tooling
Our family tooling solutions are designed to streamline production by allowing multiple related parts to be molded within a single tool.
This approach is ideal for projects requiring various components with similar sizes or shapes, reducing setup times and costs while maintaining precision and consistency across your product line. Whether you’re producing small batches or complex assemblies, our expertise ensures efficient, high-quality results tailored to your needs.
Multi-Cavity Tooling
With multi-cavity tooling, we maximize productivity by creating molds capable of producing multiple identical parts in a single cycle.
This high-efficiency option is perfect for large-scale production runs, cutting down on cycle times and optimizing output without compromising quality. Our team designs each tool with precision, ensuring uniformity across every cavity to meet your exact specifications and accelerate your time to market.
Tooling Material
We offer a range of tooling material options—such as steel, hardened steel, and aluminum—to match your project’s unique demands.
Steel and hardened steel provide exceptional durability for high-volume runs, while aluminum offers a cost-effective, lightweight alternative for shorter runs or prototypes. Our skilled team helps you select the right material based on factors like budget, production volume, and part complexity, ensuring optimal performance and longevity.
Shot Life
Shot life reflects the durability and lifespan of your mold, a critical factor in planning production efficiency and cost.
We engineer our injection mold tools to deliver impressive shot life, whether you need a mold for a few thousand cycles or millions. By leveraging advanced materials and meticulous craftsmanship, we ensure your tooling withstands the rigors of repeated use, providing reliable performance and exceptional value over time.
Value
Precision Engineering for Scalable Production
Modular tooling solutions that can be expanded or reconfigured based on evolving product lines or manufacturing needs. Capacity to scale tooling production in response to increased demand for new products or variations.
Ability to produce a wide range of tooling types for different manufacturing processes, accommodating varying production volumes. Integration of automated systems to enhance tool-building efficiency and precision, supporting higher volume requirements.
process
Concept to Completion
Step 1
DFM & Engineering
Before a mold is built, a precise design is developed based on product specifications. This step includes CAD modeling, material selection, and mold flow analysis to ensure efficiency, durability, and manufacturability.
Step 2
Tool Fabrication
Once the design is finalized, our skilled machinists use advanced CNC and EDM processes to craft the mold. Precision cutting, polishing, and assembly ensure the mold meets tight tolerances for consistent, high-quality production.
Step 3
Sampling & Validation
Before full-scale production, the mold undergoes rigorous testing, including initial sample runs and quality inspections. Adjustments are made as needed to optimize performance, cycle times, and product consistency.
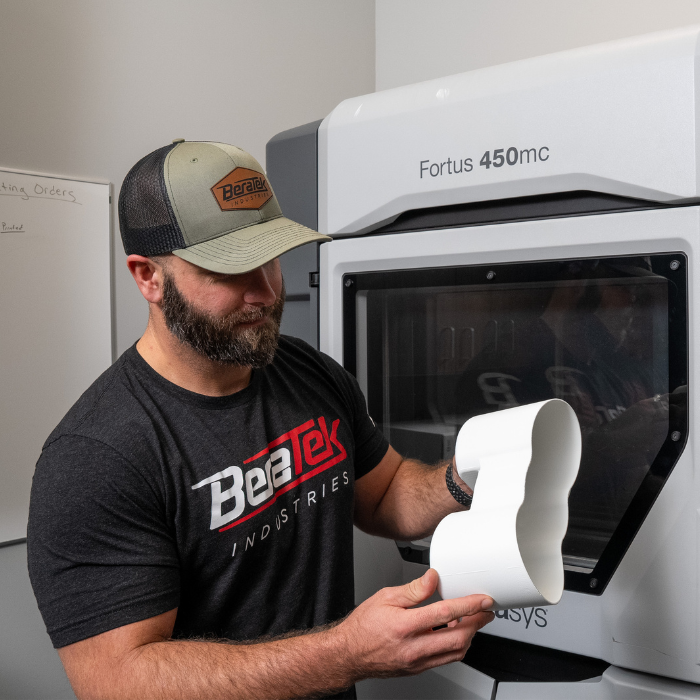
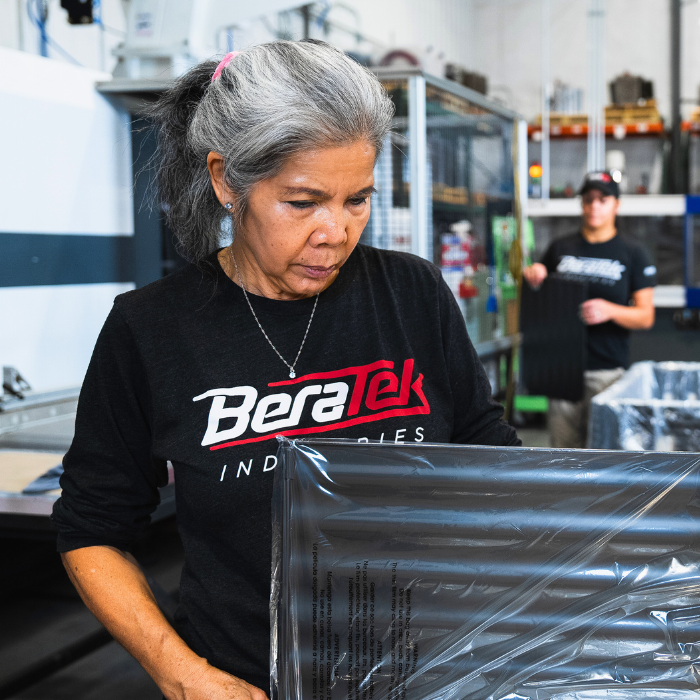
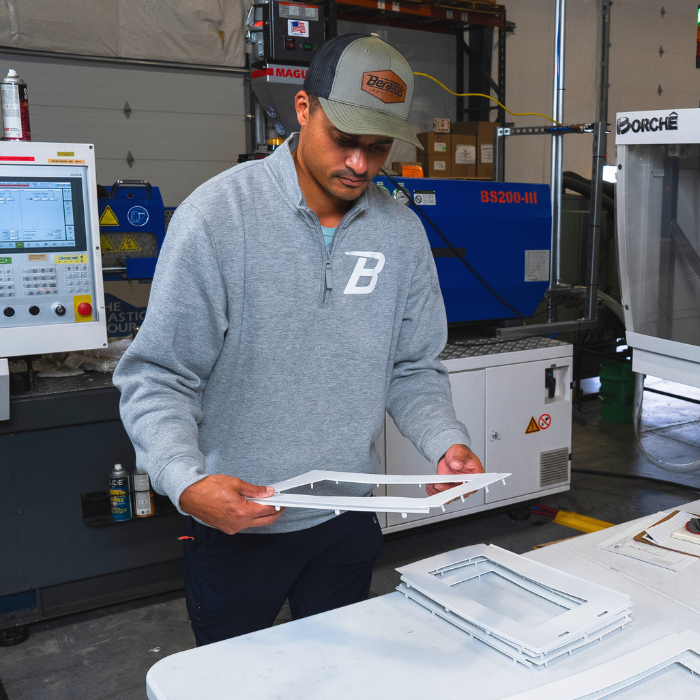