mold design
product design & engineering
Our engineering and product design team works with you to select the best materials for your production, simplify assembly operations, and improve design features for efficient production. We’ll immerse you in the process, from 3D CAD modeling and prototyping to mold design, ensuring complete transparency, precision, and a seamless development process.
Our Work
We thrive on tackling complex challenges and delivering exceptional results.
Every project is an opportunity to push the boundaries of innovation, applying our injection molding design expertise to create smarter, more efficient solutions. Whether refining an existing product or developing something entirely new, we approach each challenge with a problem-solving mindset, ensuring your vision is brought to life with precision and excellence.
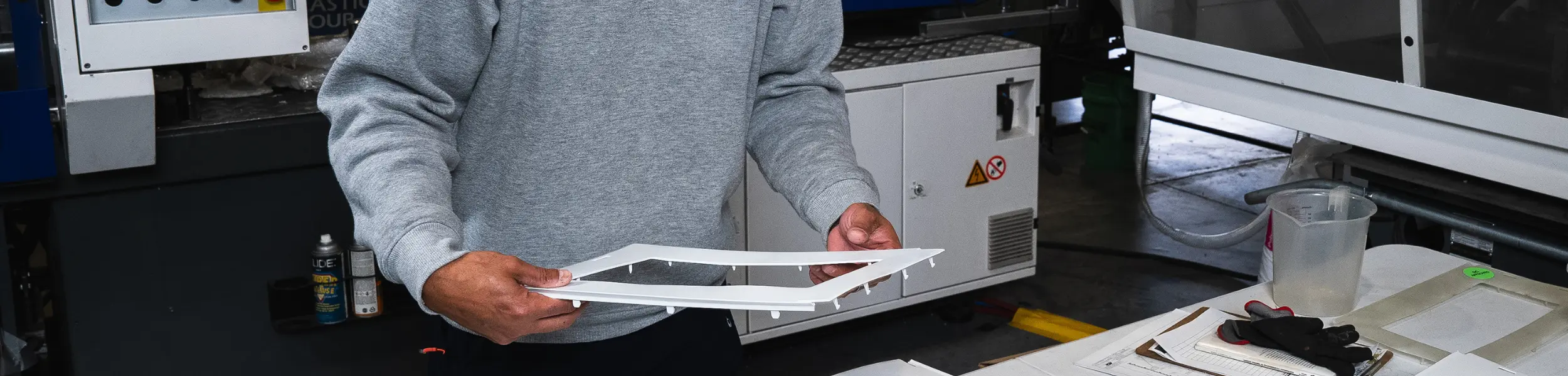
Expertise
Product Design and Engineering Services
A strong injection mold design is essential before manufacturing plastic parts. Our team brings a diverse range of technical expertise, allowing us to provide strategic recommendations that enhance the usability, functionality, and overall performance of your products.
Mechanical Engineering Expertise
With extensive expertise in plastic part development, our mechanical engineers apply advanced engineering principles and technologies. This ensures that our solutions achieve peak performance, durability, and cost-effectiveness for various applications.
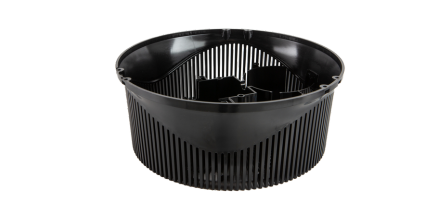
Design for Manufacturability (DFM)
Our DFM services optimize designs for cost-effective production, reducing costs and time-to-market. We analyze designs to identify and resolve issues, streamlining manufacturing processes while maintaining product integrity and performance.
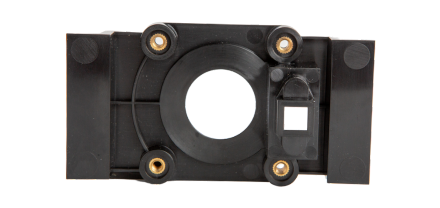
3D CAD Modeling
Utilizing state-of-the-art 3D CAD software, our designers can create detailed and accurate models of your parts. This process allows for precise visualization, simulation, and testing of designs before moving to production. Through simulation and analysis, designs can be tested for stress, thermal, and other factors, ensuring that parts perform as expected under real-world conditions.
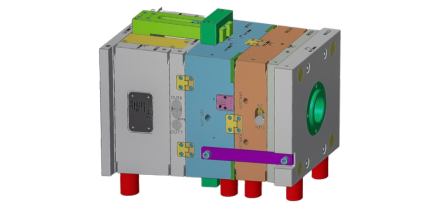
Reverse Engineering
Our reverse engineering services analyze and improve existing products, providing valuable insights into functionality and design. We meticulously deconstruct products to create enhanced versions or compatible components, staying ahead in the market.
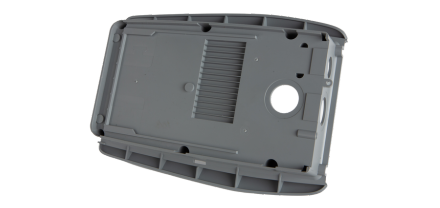
Metal to Plastic Conversion
Transitioning from metal components to plastic can offer numerous benefits, including weight reduction, cost savings, and improved manufacturing efficiency. Our team specializes in evaluating metal parts and redesigning them for plastic injection molding without compromising performance.
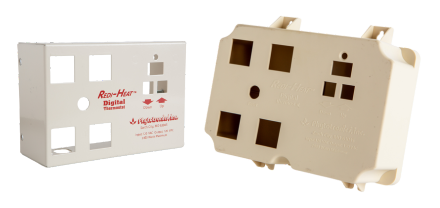
Custom Injection Molding Design Guidelines
Undercuts
Reduce undercuts, which will increase the complexity and cost of the tool ejection mechanisms, by adding in pass-thru coring.
Wall Thickness
Prevent wall sink and voids by maintaining and even wall thickness. Thinner walls reduce cycle time and reduce costs.
Drafts
Ensure parts are designed with a minimum draft angle of 0.5º, or up to 5º, for faces with medium textures.
Ribs/Gussets
Ribs should be 40-60% the thickness of outer walls and should still maintain draft.
Bosses
Bosses should be designed at a depth of 30% the wall thickness and with a 30% edge groove. Attach them to side walls or ribs for structural integrity.
Quality
Elevating Product Design for Optimal Performance
Exceptional injection molded product design is not just innovation and aesthetics, but the ability to optimize designs for efficient manufacturing processes.
Whether it’s selecting the right materials, simplifying the assembly process, or fine-tuning the design for manufacturing scalability, we’re committed to creating injection-molded products that are not only innovative but production-ready.
Process
Concept to Completion
Step 1
Concept Development & Research
We begin with brainstorming ideas, defining product requirements, and conducting market and feasibility research. Our designers and engineers collaborate to outline functionality, user needs, and material considerations.
Step 2
Detailed Design & Engineering
Using CAD software, the product takes shape with precise dimensions, material selection, and manufacturability considerations. Design for Manufacturing (DFM) principles are applied to ensure efficiency and cost-effectiveness in production.
Step 3
Prototyping & Validation
A prototype is created using 3D printing, CNC machining, or other rapid prototyping methods. The prototype undergoes functional testing, user evaluation, and refinement to validate the design before moving toward full-scale production.
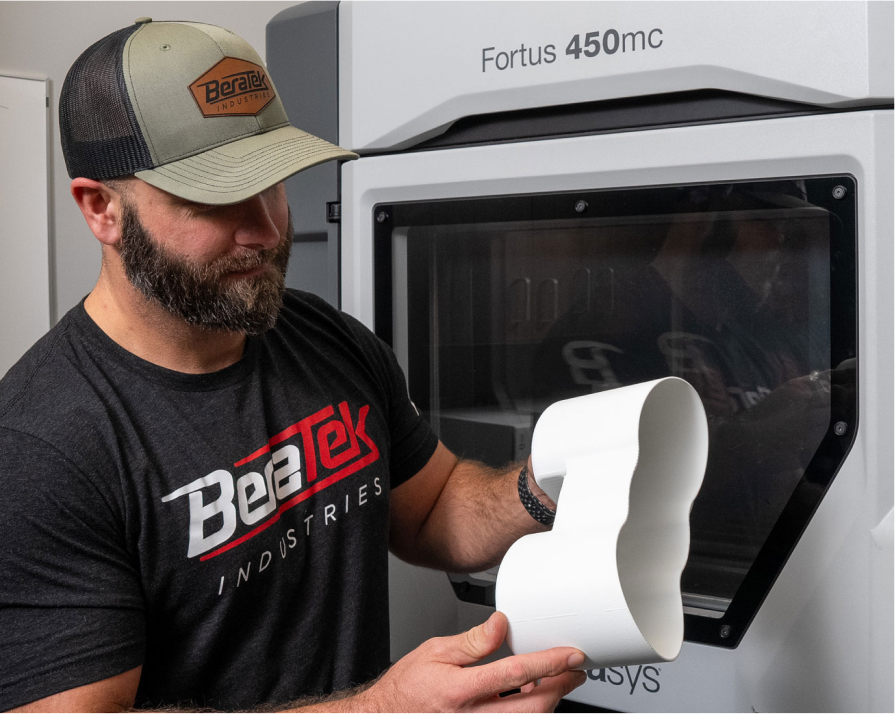
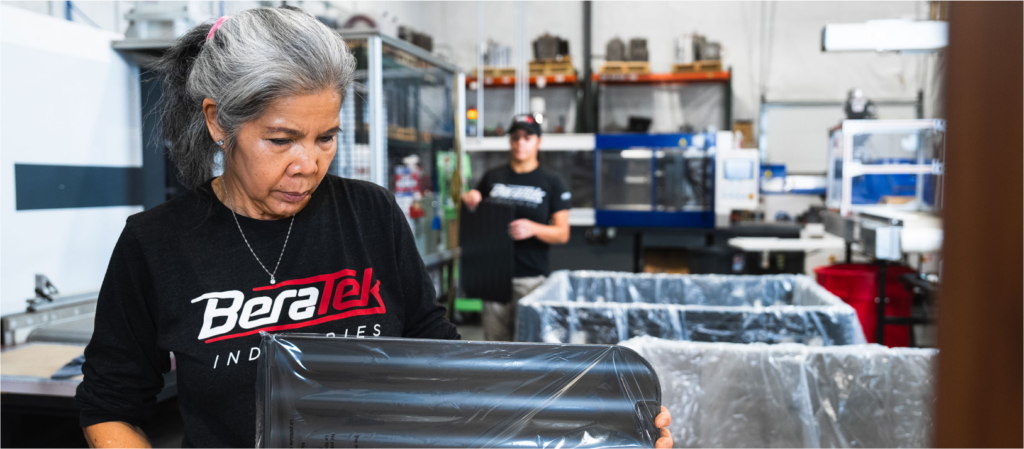
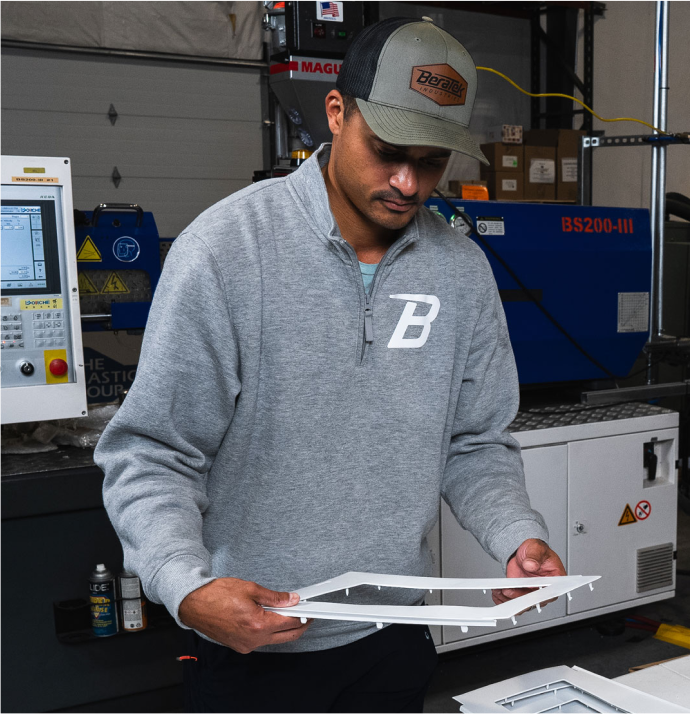